StanleyBlack&Decker Corporation
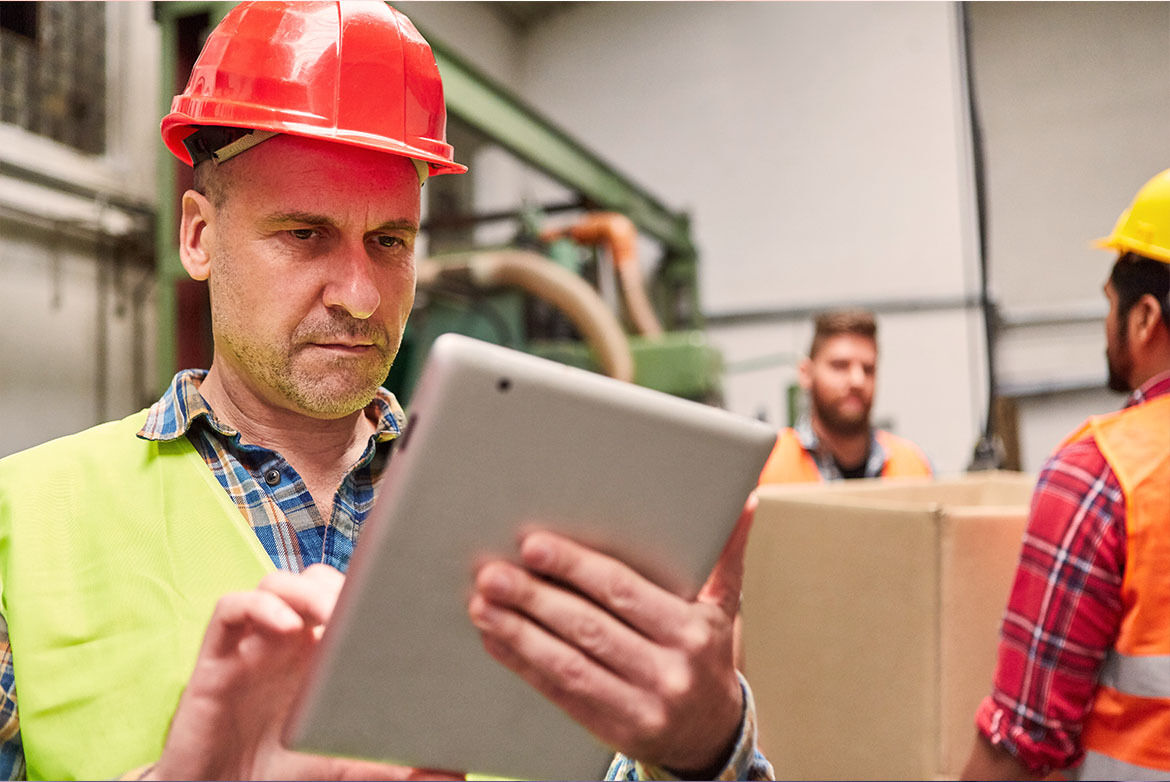
The challenge: digitizing demand requirements via an app
Tucker GmbH is part of the StanleyBlack&Decker Corporation and supplies the automotive industry with stud welding equipment, bolts, metal and plastic parts, among many other things.
As part of its digital transformation, StanleyBlack&Decker is examining their production processes as well as internal administrative processes. Their current processes in the form of paper, emails, and Excel files were to be digitized step by step and integrated into a standardized workflow environment.
Transparency, speed and cost reduction
- Transparency in process flows is achieved by ensuring compliance with regulatory and quality requirements, as well as reporting accurate data
- Acceleration in processing is achieved by eliminating manual interfaces and implementing automated reminders for open tasks.
- reducing errors
- Reduction of costs, for example through fewer reminder costs in the invoice processes and standardized differentiation between warranty cases and service cases
The process
Process modelling, pilot, digitalizationVueJS, .NET Core and BPMN 2.0 in use
The technologies used were VueJS in the frontend and .Net Core with ASP.NET Core in the backend. StanleyBlack&Decker requested that the processes be modelled in the BPMN 2.0 standard and to use a process engine. However, since they had no experience in this area, a suitable engine had to be selected at the beginning of the project.
The methods and tools were then to be tested using a pilot. The requisition process, or BANF for short, was used for this purpose. This is the implementation of a US regulation, the Sarbanes-Oxley Act (SOX), to which the US-listed company StanleyBlack&Decker is subject. Every order must be based on a valid, correctly approved requisition in accordance with the signature regulations. The requisitions and the approvals were previously carried out on paper. The turnaround times were very high and there was a lack of transparency. As part of the pilot, the paper form and the downstream approval process, including the complex rules for determining the approvers and checking the entries, were completely digitized.
Next, the complex PPAP (Production Part Approval Process, IATF 16949) process was digitized. In this process, a series parts are sampled to ensure quality. This requires, among other things, the creation or provision of various documents, the checking of parts and measurement methods, and the carrying out of material and performance tests. The implementation was internationally convincing, so in a subsequent project, the application was made multi-client capable and internationalized. It is now used by various locations of the group.
Due to the quickly visible benefits and the high level of acceptance of the process applications among employees, further processes could be tackled in subsequent projects and implemented on the Camunda platform, including the downstream process for approving invoices (SOX), the process for ordering tools and processes relating to shipments without an invoice.
"The team brings in people from all specialist areas. A special feature is that the product is developed with the user in mind. They don't come up with something that doesn't work in the application afterwards."Nicole HoffmannJunior Account Manager, Stanley
Implementation with Camunda, BPMN and Azure Cloud
Accso initially advised Stanley Black & Decker on selecting the optimal tools and technologies to ensure the digitalization of processes is both flexible and future-proof.
As part of a market study, Accso evaluated various process engines based on criteria such as scalability, interfaces, testability, migration and error handling, as well as usability and support. The Camunda platform (Camunda 7) excelled in all categories.
After the successful completion of the pilot, Accso gradually specified the further processes together with the customer using an agile approach (Scrum), modelled them in BPMN 2.0 and implemented them on the Camunda platform. The integration of IT systems from Tucker GmbH, such as the ERP system, also played a major role.
All digitized processes run in the form of applications in the Azure Cloud. Accso was also able to provide support and created the necessary infrastructure and an automated deployment process with Azure DevOps to automatically deploy the applications and parts of their infrastructure components.